The workshop is undergoing a fairly massive rearrange at the moment in an attempt to create a bit more workable space whilst at the same time accomodating some more machines to expand its capabilities.
For many years I've run the workshop with two lathes, originally a Colchester Bantam and Triumph 2000, with a Chipmaster replacing the Bantam in recent times. It is fair to say that the Triumph gets to do less work than the smaller machine, but when it is needed, nothing else will do. Plus I enjoy using it. Which makes it even more unfathomable why, when friend Joe needed a big lathe last year and asked if I wanted to sell it, I said yes. Possibly it was because at the time it was in the unit next door, awaiting recommissioning after the move, possibly because he caught me at a time when I hadn't got anything big to turn. Whichever way, he took it (and has put it to good use ever since) and I have regretted its disposal every month when I have to run across the road to get large things turned at the precision engineers opposite.
Having regretted its disposal for the last year, when a local company replaced their Triumph with a new Tornado CNC machine, I bought it virtually before the spindle stopped turning (they had it on pretty constant production work - it was still earning its keep the morning I collected it). It's almost the same as the last one, grubby but still accurate (which is pretty typical of most Triumphs), complete with Ainjest high speed threader (which I rated highly on the old machine) and a DRO (which I've never had on a lathe before, I'll just have to get used to these new-fangled gadgets).
The last time I bought a new machine was the Bridgeport EZ-Trak mill, about seven years ago. It's still in constant use, is an immensely versatile machine and is pretty much ideal for one-off prototyping and small batches of components. It has two axis CNC control, three axis DRO - basically it needs an operator (me) to operate the quill for Z moves and change tools. This is hardly an onerous task, but does require fairly constant attendance unless it is doing a long cycle at a constant depth setting - machining out expansion links usually gives me twenty minutes where I can be doing productive work elsewhere (or grabbing a coffee and nattering to Karl next door...).
Having deliberated for some time about a new machine, I have finally bought a new mill to run alongside the Bridgeport, a vertical machining centre this time, which is a much faster, fully 3D machine with a 10 station tool changer.
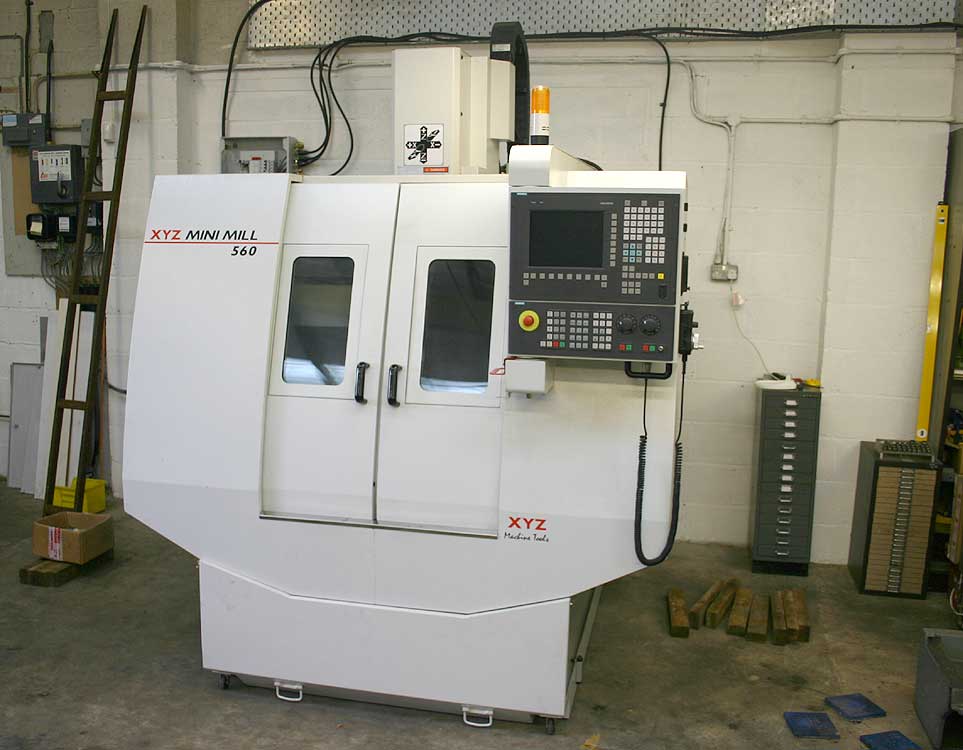
It was delivered a couple of weeks ago - at just over three tons it's not something I can easily move around in the workshop, so let the professional machine movers crane it in and then put it in position using a pair of sixteen ton capacity skates.
In the time-honoured fashion, having brought two new machine into the workshop, I've convinced myself that with a little judicious tidying up and rearranging, I'll actually end up with more floor space than I had before. It is actually starting to look tidier, but it still needs a little fine tuning. I'll post some pictures next time to show how successful the new layout turns out to be.